Scottsdale’s new generation of C-Section roll forming machines are now available and provide extra grunt, safety and performance for steel framing and fabrication. Several enhancements, including extra machine speed, deliver savings in operator time, steel usage and safety.
Fully integrated within the Scottsdale ecosystem, these latest roll formers perform all the functions of Scottsdale’s first generation, but at speeds and functionality that can take your steel operations to a new dimension.
Whether you’re a high-volume fabrication plant operator or a busy builder needing to punch out frames on site, the new generation of machines from Scottsdale will more rapidly produce components completely ready for easy assembly.
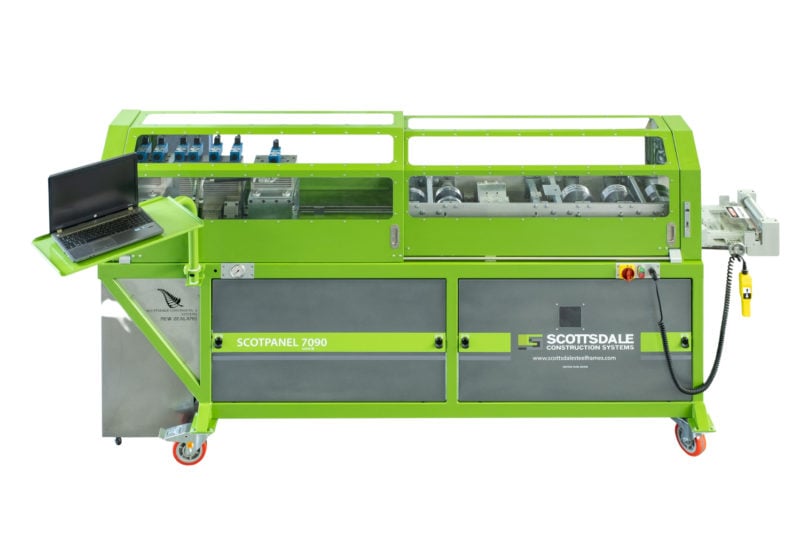
What’s Changed?
The new generation machines now come in two versions — a Standard model and a GEN II — both with significant upgrades over the previous range that offer:
Speed — Up to 25% faster output
An increase in drive sprocket combined with gearbox ratio reduction boosts the new drive’s speed and performance by up to 25%. Up to 1,500 metres of rolled steel per hour.
Savings — Time saving roller adjustment and coil guidance
Automatic self-adjusting rollers save time having to set correct roller pressure whenever a different gauge of steel coil is used. Together with an enhanced in-feed guiding system that centres the coil in the roller and gives greater stability and less machine stress, this all adds up to bottom line savings.
Strength — Releases full stud compressive strength
The new end bearing guillotine in the toolhead allows the stud to sit flush in the bottom and top track of wall frames. This means the true stud compressive strength can be fully utilised, surpassing the connection capacity limit of studs when running engineering analysis, ultimately giving sturdier construction while saving on materials.
Safety — Now with enhanced protective frame
Bottom and top casing panels and top sliding panels provide a safer environment, preventing objects or operators from coming in contact with the working parts of the machine. The sliding top gives operators easy access when required.
Plus, like other machines in the Scottsdale ecosystem, these latest models are also:
Smarter — backed up by our latest software developments, with improved engineered designs that use less steel.
Sharper — precision enhanced to within 0.1mm, the thickness of a builder’s fingernail.
Smoother — Easy to learn and use, with Scottsdale’s training and setup, business know-how and operational support, plus 24/7 service and repair.
The Scottsdale Ecosystem
Scottsdale’s total steel fabrication “ecosystem” comprises the necessary hardware, software and support that together allow us to help our customer success in operating and growing successful steel fabrication operations. The ecosystem includes:
- Panel and truss roll forming machines
- Design, engineering and roll forming software
- 24/7 support service
- Business setup, know-how and operational support
- cut to length
- notch punch
- swage
- squash
- rivet punch
- service hole punch
- optional Plumbing Notch Tool
Also supplied
- powered decoiler
- Scot-Panel CNC software
- latest ScotSteel CAD design software
Specifications
Panel:
- Gearbox 12.5:1
- 17th drive sprocket
- Infeed Guide Unit
- Self Adjusting Rollers
- Bottom Covers
- Sliding Top Covers
- New Frame
- New swage tool, allowing for a smoother joint
- Steel sensor to avoid potential damage to the encoder
- Temperature sensor to allow for fluctuations in temperature which could affect calibration
- Larger radiator
- Larger accumulator
- Larger oil tank
- Larger hydraulic pump
- New age de-coiler which can take a master coil of 1,500 kgs
- Waste bin attached to the front of the frame
Toolhead:
- End Bearing Guillotine
Cabinet:
- Isolating switch on the outside of frame
- Handheld Forward and Reverse Pendant
For more information on the new range of roll formers, including detailed specification, pricing and availability, get in touch with our team.